News
Silicone mold
- 2016-09-23 18:15:46
-
Edit silicone moldSilicone mold generally consists of the gum base, crosslinking agents, catalysts, fillers and additive component comprises five generally gum base, crosslinking agents and fillers are made of a component, and the catalyst as a separate component, it has silicone mold It is called two-component cured silicone, RTV-2 silicone RTV. Which cure at room temperature, the compound of two main plastic component was added (1% -5%) amount of catalyst (curing agent) to generate cross-linking reaction is formed with a flexible, resilient gel.Chinese name English name mold silicone Mold silicone applications craft gift industry, construction and decoration industries hardness of 0 ° --50 ° (according to demand adjustment) Use the product copy and mold makingtable of Contents1 uses silicone mold2 silicone mold selection3 of structural silicone mold4 Characteristics of silicone moldProduction Method 5 silicone moldsThe method of operation silicone mold7 application of common problems encountered? less turning model number? burning mode phenomenon appearsProduction methods ? mold filling and mold fragments? quit phenomenon occurs in dry form? poor phenomenon appears Rally? not die acid, intolerant aging? surfaces of the molding marks, streaks and rough and so? How plating silicone mold cleaning8 condensation silicone mold silicone mold and processing What is the differenceSelect 9 silicone mold mold mode selection, and analog lines10 Market ProspectsUse of silicone mold editMainly used for toy and gift industry, craft gift industry, furniture decoration industry, figure copying, building decoration industry, resin handicraft industry, unsaturated resin crafts industry, candles ? plastic toy industry, gift stationery industry ? ?, gypsum gifts industry, ? mold manufacturing industry, ? Boli industrial ?, simulation of animals and plants sculpture, Buddhist carvings and other crafts products industry replication and mold making.Select Edit silicone moldDepending on the operating mode, if the perfusion mode (packet mode) can be used hardness of 20 degrees or 40 degrees of silica gel, specifically that:20 degrees of hardness silicone mold features: a small piece of handicraft, small viscosity, good liquidity, good operation, easy to row bubble, good tensile tear strength, easy to perfusion.40 degrees of hardness silicone mold features: bigger products, small viscosity, good liquidity, good operation, easy to row bubble, good tensile tear strength, easy to perfusion.Structure Editor of silicone moldSilicone mold generally consists of the gum base, crosslinking agents, catalysts, fillers, additives and five component composition. In theory, as long as the first three components can be made of silicone mold, but to get some strength, "packing" is generally necessary, and "filled with PPD," as the case may be, section. Typically gum base, crosslinking agents and fillers are made of a component, and the catalyst as a separate component. The catalyst component of the main rubber component ratio is generally between 1% -3%, the catalyst can be adjusted by adjusting the ratio of crosslinking reaction speed.Edit properties of silicone mold① silicon rubber mold to have a good operating performance.② silica gel for better flow, low viscosity easy to operate.③ silicone rubber shrinkage as small as possible.Rally ④ silicone rubber better.⑤ made out of silicone mold can not be deformed.⑥ silicone rubber hardness should be suitable for production use.⑦ high temperature, turning model more often, the longer the better life, acid and alkali resistance to aging.Silicone mold manufacturing method editor1, a plastic bowl filled with 500g gel, curing agent at room temperature for 1.5 percent, stir spare.2, the mother mold material treated with a release agent lubrication.3, lubrication good mother blanks surrounded by wood surrounds, wood processing release agent is also applied, in the middle of the gap to 2-4cm appropriate.4, with a good glue along a fixed perfusion slowly pouring point is not to eliminate the shock when the air inside.5,60 minutes glue completely cured after four weeks and then surrounded by strips of wood, leaving 4cm gap, demolition wood strips.6, after the injection of gypsum powder 1000g watered wooden box, filled up (wooden frame application plastic film into two parts to facilitate form removal).7.20 minutes after the removal of wood, mold that is made complete.Precautions:1, plus the amount of the curing agent should be, depending on temperature, the high temperature is reduced. Curing agent is used in excess, will harden brittle mold; curing agent is too small, the operating time is extended.2, to prevent mold silicone material changes, we recommend without silicone oil.3, in order that you can mold to achieve the best results, the mold storage for at least 24 hours after use.4, the die can also be made of resin.Operation of editing silicone mold1, silicone and curing agent Stir liquid silicone mold appearance is flowing, A component is silica, component B is the curing agent. Example: Take 100 grams of silica gel, 2 g of curing agent (Note: Be sure to silicone and curing agent Stir, stir if not, there will be a mold has been cured, a not cured, dried and cured silicone will appear uneven situation on silicone mold will affect the life and turning model number, even resulting in mold scrapped situation.2, vacuum row bubble treatment: silicone and curing agent Stir evacuated discharge bubbles link, vacuum time should not be too long, under normal circumstances, not more than ten minutes, vacuum for too long, silicone immediately curing, resulting in a crosslinking reflect that into a piece of silicone can not be painted or perfusion, thus wasting silica, silica gel can only put into the trash, do re-take the silica gel.3, brushing or procedure: the evacuated discharge bubbles through silica gel, brushing or perfusion mode. Pour the product above (NOTE: The product or model to be copied down before silicone release agent or release agent is absolutely necessary). Then put in the product above silicone brushing, brushing must be uniform, 30 minutes after you paste a layer of gauze fiber silicone sheeting to increase the intensity and tension. Then brushing a layer of silica gel, and then paste a layer of gauze fiber sheeting, after so twice on it. Only in this way, open up the silicone mold turning model of life and to improve the lot number of a relative, it can save costs and improve efficiency.4, the outer mold production: general methods and materials are used to mold around with a plastic sheet or boarded up, a cabinet filled with plaster to mold it, another way of using the resin brushing, brushing layer on layer of resin paste fiberglass cloth, then brushing then paste, repeated two or three to complete the outer mold die.5. The method of operation mold filling or perfusion mode: mold filling or perfusion mode, is used to smooth or relatively simple product, there is no parting line saving time and labor,6, mold or sheet molding fragmentation methods of operation: first before brushing your product or model to be copied brushing a layer of release agent or release agent), wait 30 minutes, the surface layer of gauze or glass paste after sheeting to increase fiber strength, and then brushing the second layer of silica gel silica gel drying, do the outer mold, the outer mold can use the plaster or resin materials.Common problems encountered in the application editorTurning model of fewerMold in the production process of adding too much silicone oil, silicone oil destroyed the molecular weight of the silica, so the mold will be turning model of fewer non-durable and so on. If the products do little more complex pattern of products, with a large open-hardness silica occurs turning model of fewer phenomenon, because the silicone perfect time will be very brittle, easily broken. Conversely, if you do build products with a small hardness silicone mold to do, the result will also be unsatisfactory. Because the silicone is too soft, it will reduce the tensile and tear strength, made out of the mold will be deformed, so turning model number will be reduced. Plastic mold itself are very good quality, silicone not good or bad, only the fit and do not fit. We want to use for the size of the product hardness silicone to make the mold will not appear the situation.Burn-in phenomenon moldBecause unsaturated resin and the resin product plus a peroxide curing agent after the reaction resin case will generate a lot of heat, general resin curing time of 3 minutes, so 3 minutes to release as soon as possible, we will not be able to prevent the silicone mold produce burning mode phenomenon.Production methods mold filling and mold fragmentsSlicing the mold or sheet molding method of operation: the smoked vacuum silica gel brushing or pouring methods of construction. If you do die sheet or slice mold has adopted brushing way, before brushing first layer of release agent or release agent on the product you want to copy or model brushing, then brushing the silicone in the product above (note : be sure to brush evenly), wait 30 minutes, the surface of the paste layer of gauze or glass fiber cloth to increase the intensity, and then coated with a second layer of silica, silica gel drying, etc., do the outer mold, the mold can be used outside plaster or resin material.Operation mold filling or perfusion mode: mold filling or perfusion mode, is used to smooth or relatively simple product, is the product or model you want to copy, with a plastic sheet or a glass enclosed, will be pumped through the vacuum of silica gel directly into the products above, to be dried silicone molding, remove the product, the mold on the shape (Note: perfusion mode generally used hardness is relatively soft silicone mold to do, so the release easier, silicone mold will not damage the inside of the product) the above is the whole process of mold silicone use and operation.Tack phenomenon appears in quitSilicone mold belongs condensation silicone, it is by absorbing moisture from the air and cured silicone in the process of making, the water evaporated, while not transferred amount of water, this phenomenon occurs . Solution: This phenomenon does not belong to product quality issues, but because there is no control of water, lifting silicone shelf life, shelf life for a long time to appear these phenomena, as long as when using silica gel, adding an appropriate amount of 0.05% of water, stir it you can solve some of the situation.Rally difference phenomenonBecause the customer in the production process of the mold in order to reduce the viscosity of the silicone, silicone easy to make large amounts of silica in a silicone oil is added, which would make the silica gel becomes soft, tensile produce intolerance, reduced tear strength, Rally deterioration phenomenon, resulting mold is not durable, life is short, less turning model number and so on.Silicone mold itself is not Mao, there Maoyou because during operation adds composite silicone oil (silicone oil and white mineral oil complex ligand) as white mineral oils are petrochemical products, not silicone.Mold is not acid, intolerant agingIn the process of making silicone mold, we recommend that customers with the best without any silicone oil, if desired, the amount of silicone oil added up to no more than 5% to 10%. Because of the excessive amount of silicone oil will destroy the molecular weight of the silica, so out of the mold will produce acid, intolerant aging phenomenon.Surfaces of the molding marks, streaks and rough and soThis phenomenon is the product or model to be copied no grinding or polishing sake. Because in fact the model or the product itself is not smooth enough or perfect, so the product or model to be copied if not polished or polished, even the best silicone mold will do pretty, it is not smooth enough. Another case is, when the release agent in the fight, not even brushing can also cause mold is not smooth.How plating silicone mold cleaningElectroplating mold can not go to be cleaned with ordinary sand blasting method, should be using a local dirt cleaning, is generally used to clean up those individual parts plating mold accumulated dirt needs to be cleaned, if it is the mold from the vulcanizing machine removed, then it is more a waste of time this time we just through chopsticks, long strips of wood and other small wooden stuff to scrape the dirt inside the cavity, the use of wood stuff to remove the dirt because of the hardness of the wood is relatively low, it will not hurt the surface of the mold silicone products pure water to dilute the same time we can with the amount of caustic soda plus 10 times, and then take a cotton swab dipped in dilute aqueous base sheet to wipe the dirt to fall off; plating layer.Or go full-mold dirt cleaning method, plating mold on the silicone products vulcanizing agent or an oven heated to 160 ℃, and then press the caustic soda and water ratio of 1: 100 of the caustic soda into the boiling water and mix well, then will pour in the liquid with a good mold, while copper brush to wash dirt off so that the cavity surface, brushing process continues pouring liquid, to avoid mold and dried. After the scrub clean, flush with water mold, so that the liquid is completely clean, air gun and then quickly dry the mold surface water. The entire operation should wear protective gloves to avoid scalding.Condensation silicone mold silicone mold and processing What is the difference editorCondensation-type silicone mold can be cured at room temperature, 8-24 hours into the elastomer. You can accelerate the increase in the amount of curing agent. The increase or decrease in the curing agent. Higher temperatures and humidity, curing faster.Plus RTV silicone mold: condensation-type silicone mold lower strength, the latter a higher strength. Its mechanism is based on silicon hydrogen sulfide vinyl (or allyl) silicone raw rubber end groups and the crosslinking agent molecules on the addition reaction (hydrosilation reaction) to complete. In this reaction, containing a hydride-functional polysiloxane is used as crosslinking agent (curing agent) chloroplatinic acid or other soluble platinum compound used as a catalyst. Sulfurization reaction is carried out at room temperature. It does not release byproducts. Since the cross-linking process does not release low molecular weight compounds, so add molding RTV silicone rubber does not produce contraction in the vulcanization process. This class of vulcanized rubber, non-toxic, high mechanical strength, excellent hydrolytic stability (even under high-pressure steam), a good low compression set, low flammability, the depth of cure, and cure rate can be used to control the temperature, etc. advantages, it is a kind of silicone rubber at home and abroad to develop, in addition, to change the amount of curing agent, curing speed will not change, but will affect the physical properties after curing is complete. Therefore, the measurement of the curing agent must be done as accurately as possible.Select Edit mode mold silicone mold and die selection linesSelect the choice of form and mold parting line is very important,First, in order to facilitate moduloSecond, the parting line should be selected without affecting the overall effect of the productThird, do not affect the quality of products, such as water features series-mode line position is too high, seal the parting line when the material to be more prone to cracking products; fourth is to reduce the flow of operating procedures, such as open mold half.To prevent the flow around the silicone mold species with a wooden plank or a fixed rule in the range, when the opening piece mold with wood and sludge separated that part of the first to open, requiring between sludge and mold species no gap, sludge surface smooth. After the above-mentioned preparation work completed, followed by plaster mold or mold species coated with petroleum jelly or spray release agent on smooth product requirements with a clean cotton cloth soaked in Vaseline evenly coated in the mold species, held for 30 minutes to die kind fully absorb Vaseline, and then a clean cotton cloth to clean the surface of the mold species require bright surface; and as long as the product has a texture evenly coated with Vaseline on it will be better formulated silicone tune. When silica gel formulations should be random directions while stirring, a curing agent and silicone mix thoroughly to minimize the air mixed in gel, smooth product is best applied when the vacuum pump once the first layer of glue, holding the vacuum requirement -0.1Mpa 7-8 seconds.Silica gel with a good timely molding. The glue in a way trickle down in the highest parts of the mold species, let the natural flow, flow not in place by painting brush in place, if the piece is not only full of mold silicone brush evenly throughout the product but also on clay. Each product brush at least three layers each layer of silica silica thickness of 1mm, silica gel in the brush process, requires curing after each layer to another layer of the brush when the brush is applied to the third layer on top of a second layer layer of gauze to increase the strength of the silica gel. The entire mold silicone products based in part on the size of the different requirements for thickness control in 3-4mm, width no greater than the product width 60mm. Silicone start setting time was 20 minutes.1, the master mold dry cleaned, for the smooth handling (can play a layer of mold release wax or brush one release agent)2, 500-1000 g of silicon rubber mold (silicone mold, plastic mold, silicone rubber, silicone) Sheng such as plastic pots spare;3, after the hardener by weight ratio (typically 1.5-2.5%) were weighed into a container for mixing, stir;4, depending on the situation (in particular, the first layer) by adding a certain amount of silicone diluent. Until thoroughly mixed so far, usually 3-5 minutes.5, mixing silicon rubber mold (silicone mold, plastic mold, silicone rubber, silicone) and hardener, the reaction was carried out at room temperature, that is, and the release of low molecular weight alcohol, the alcohol molecules from the colloid as required under negative pressure discharge bulbs 1 -3 minutes. Also available (depending mainly depends mold division operating experience) without the aid of the device 6, the multilayer sheet molding brushing should follow the inner, middle and outer while curing is appropriate. Curing agent is relatively small, the reaction time is lengthened, the full response, colloid like, thus curing agent is preferably within less foreign and more. Brushing until the first layer (inner layer) dry and then brush the second layer. Operating time 30-50 minutes, the removal time 10-15 hours. Curing time of 24 hours. Note brushing first, such as gauze after the best two-story addition, which can greatly improve the mold life (but must not use fiberglass cloth, or likely to cause the hierarchical leaving the entire mold scrapped)7, three-dimensional perfusion mode, generally 10-15 hours curing as well.8, but also of plaster or fiberglass outer mold produced after soft to support the soft silicone moldnote:1, line selection mode: Select position does not affect the appearance of the product; choose a location after grouting easy processing; mold itself is easy to select the form removal position; select the product easily deformed position2, must not be in a hurry to increase the amount of the production schedule and blind hardener, otherwise it will greatly reduce the life of the silicone mold.Market outlook editState silicone downstream industry development present polarization. The presence of silicone monomer in the domestic anti-dumping protection policy context, in recent years, domestic enterprises launched a large monomer production capacity, these products can enter the concentration of the release period in 2009-2012, industry monomer production capacity phased excess; but the downstream deep-processing product development is slow , thus making the downstream processing enterprises continue to get high profitability, while different from the international market in an integrated enterprise-based industry characteristics.From the development path of the domestic enterprises in terms of silica gel, single monomers and intermediates business is difficult to achieve sustained and stable development, we can not avoid the impact of price volatility. After obtaining competitive advantage and the ability to have the financing to complete the layout of the leading enterprises in the field of the monomers, are actively expanding downstream products. Future enterprises Monomer / Intermediate internal digestion ratio will increase substantially corresponding to a monomer / intermediate amount of goods will be significantly reduced, and the transfer of profits from the industry to the whole field of downstream processing industry comprehensive income, profitability and integration ability to hedge risk gradually. With the rapid development of the domestic industry, the demand will increase the mold, silicone mold market potential will increase!Entry Label:Non-life, life, industrial productsEdit silicone moldSilicone mold generally consists of the gum base, crosslinking agents, catalysts, fillers and additive component comprises five generally gum base, crosslinking agents and fillers are made of a component, and the catalyst as a separate component, it has silicone mold It is called two-component cured silicone, RTV-2 silicone RTV. Which cure at room temperature, the compound of two main plastic component was added (1% -5%) amount of catalyst (curing agent) to generate cross-linking reaction is formed with a flexible, resilient gel.Chinese name English name mold silicone Mold silicone applications craft gift industry, construction and decoration industries hardness of 0 ° --50 ° (according to demand adjustment) Use the product copy and mold makingtable of Contents1 uses silicone mold2 silicone mold selection3 of structural silicone mold4 Characteristics of silicone moldProduction Method 5 silicone moldsThe method of operation silicone mold7 application of common problems encountered? less turning model number? burning mode phenomenon appearsProduction methods ? mold filling and mold fragments? quit phenomenon occurs in dry form? poor phenomenon appears Rally? not die acid, intolerant aging? surfaces of the molding marks, streaks and rough and so? How plating silicone mold cleaning8 condensation silicone mold silicone mold and processing What is the differenceSelect 9 silicone mold mold mode selection, and analog lines10 Market ProspectsUse of silicone mold editMainly used for toy and gift industry, craft gift industry, furniture decoration industry, figure copying, building decoration industry, resin handicraft industry, unsaturated resin crafts industry, candles ? plastic toy industry, gift stationery industry ? ?, gypsum gifts industry, ? mold manufacturing industry, ? Boli industrial ?, simulation of animals and plants sculpture, Buddhist carvings and other crafts products industry replication and mold making.Select Edit silicone moldDepending on the operating mode, if the perfusion mode (packet mode) can be used hardness of 20 degrees or 40 degrees of silica gel, specifically that:20 degrees of hardness silicone mold features: a small piece of handicraft, small viscosity, good liquidity, good operation, easy to row bubble, good tensile tear strength, easy to perfusion.40 degrees of hardness silicone mold features: bigger products, small viscosity, good liquidity, good operation, easy to row bubble, good tensile tear strength, easy to perfusion.Structure Editor of silicone moldSilicone mold generally consists of the gum base, crosslinking agents, catalysts, fillers, additives and five component composition. In theory, as long as the first three components can be made of silicone mold, but to get some strength, "packing" is generally necessary, and "filled with PPD," as the case may be, section. Typically gum base, crosslinking agents and fillers are made of a component, and the catalyst as a separate component. The catalyst component of the main rubber component ratio is generally between 1% -3%, the catalyst can be adjusted by adjusting the ratio of crosslinking reaction speed.Edit properties of silicone mold① silicon rubber mold to have a good operating performance.② silica gel for better flow, low viscosity easy to operate.③ silicone rubber shrinkage as small as possible.Rally ④ silicone rubber better.⑤ made out of silicone mold can not be deformed.⑥ silicone rubber hardness should be suitable for production use.⑦ high temperature, turning model more often, the longer the better life, acid and alkali resistance to aging.Silicone mold manufacturing method editor1, a plastic bowl filled with 500g gel, curing agent at room temperature for 1.5 percent, stir spare.2, the mother mold material treated with a release agent lubrication.3, lubrication good mother blanks surrounded by wood surrounds, wood processing release agent is also applied, in the middle of the gap to 2-4cm appropriate.4, with a good glue along a fixed perfusion slowly pouring point is not to eliminate the shock when the air inside.5,60 minutes glue completely cured after four weeks and then surrounded by strips of wood, leaving 4cm gap, demolition wood strips.6, after the injection of gypsum powder 1000g watered wooden box, filled up (wooden frame application plastic film into two parts to facilitate form removal).7.20 minutes after the removal of wood, mold that is made complete.Precautions:1, plus the amount of the curing agent should be, depending on temperature, the high temperature is reduced. Curing agent is used in excess, will harden brittle mold; curing agent is too small, the operating time is extended.2, to prevent mold silicone material changes, we recommend without silicone oil.3, in order that you can mold to achieve the best results, the mold storage for at least 24 hours after use.4, the die can also be made of resin.Operation of editing silicone mold1, silicone and curing agent Stir liquid silicone mold appearance is flowing, A component is silica, component B is the curing agent. Example: Take 100 grams of silica gel, 2 g of curing agent (Note: Be sure to silicone and curing agent Stir, stir if not, there will be a mold has been cured, a not cured, dried and cured silicone will appear uneven situation on silicone mold will affect the life and turning model number, even resulting in mold scrapped situation.2, vacuum row bubble treatment: silicone and curing agent Stir evacuated discharge bubbles link, vacuum time should not be too long, under normal circumstances, not more than ten minutes, vacuum for too long, silicone immediately curing, resulting in a crosslinking reflect that into a piece of silicone can not be painted or perfusion, thus wasting silica, silica gel can only put into the trash, do re-take the silica gel.3, brushing or procedure: the evacuated discharge bubbles through silica gel, brushing or perfusion mode. Pour the product above (NOTE: The product or model to be copied down before silicone release agent or release agent is absolutely necessary). Then put in the product above silicone brushing, brushing must be uniform, 30 minutes after you paste a layer of gauze fiber silicone sheeting to increase the intensity and tension. Then brushing a layer of silica gel, and then paste a layer of gauze fiber sheeting, after so twice on it. Only in this way, open up the silicone mold turning model of life and to improve the lot number of a relative, it can save costs and improve efficiency.4, the outer mold production: general methods and materials are used to mold around with a plastic sheet or boarded up, a cabinet filled with plaster to mold it, another way of using the resin brushing, brushing layer on layer of resin paste fiberglass cloth, then brushing then paste, repeated two or three to complete the outer mold die.5. The method of operation mold filling or perfusion mode: mold filling or perfusion mode, is used to smooth or relatively simple product, there is no parting line saving time and labor,6, mold or sheet molding fragmentation methods of operation: first before brushing your product or model to be copied brushing a layer of release agent or release agent), wait 30 minutes, the surface layer of gauze or glass paste after sheeting to increase fiber strength, and then brushing the second layer of silica gel silica gel drying, do the outer mold, the outer mold can use the plaster or resin materials.Common problems encountered in the application editorTurning model of fewerMold in the production process of adding too much silicone oil, silicone oil destroyed the molecular weight of the silica, so the mold will be turning model of fewer non-durable and so on. If the products do little more complex pattern of products, with a large open-hardness silica occurs turning model of fewer phenomenon, because the silicone perfect time will be very brittle, easily broken. Conversely, if you do build products with a small hardness silicone mold to do, the result will also be unsatisfactory. Because the silicone is too soft, it will reduce the tensile and tear strength, made out of the mold will be deformed, so turning model number will be reduced. Plastic mold itself are very good quality, silicone not good or bad, only the fit and do not fit. We want to use for the size of the product hardness silicone to make the mold will not appear the situation.Burn-in phenomenon moldBecause unsaturated resin and the resin product plus a peroxide curing agent after the reaction resin case will generate a lot of heat, general resin curing time of 3 minutes, so 3 minutes to release as soon as possible, we will not be able to prevent the silicone mold produce burning mode phenomenon.Production methods mold filling and mold fragmentsSlicing the mold or sheet molding method of operation: the smoked vacuum silica gel brushing or pouring methods of construction. If you do die sheet or slice mold has adopted brushing way, before brushing first layer of release agent or release agent on the product you want to copy or model brushing, then brushing the silicone in the product above (note : be sure to brush evenly), wait 30 minutes, the surface of the paste layer of gauze or glass fiber cloth to increase the intensity, and then coated with a second layer of silica, silica gel drying, etc., do the outer mold, the mold can be used outside plaster or resin material.Operation mold filling or perfusion mode: mold filling or perfusion mode, is used to smooth or relatively simple product, is the product or model you want to copy, with a plastic sheet or a glass enclosed, will be pumped through the vacuum of silica gel directly into the products above, to be dried silicone molding, remove the product, the mold on the shape (Note: perfusion mode generally used hardness is relatively soft silicone mold to do, so the release easier, silicone mold will not damage the inside of the product) the above is the whole process of mold silicone use and operation.Tack phenomenon appears in quitSilicone mold belongs condensation silicone, it is by absorbing moisture from the air and cured silicone in the process of making, the water evaporated, while not transferred amount of water, this phenomenon occurs . Solution: This phenomenon does not belong to product quality issues, but because there is no control of water, lifting silicone shelf life, shelf life for a long time to appear these phenomena, as long as when using silica gel, adding an appropriate amount of 0.05% of water, stir it you can solve some of the situation.Rally difference phenomenonBecause the customer in the production process of the mold in order to reduce the viscosity of the silicone, silicone easy to make large amounts of silica in a silicone oil is added, which would make the silica gel becomes soft, tensile produce intolerance, reduced tear strength, Rally deterioration phenomenon, resulting mold is not durable, life is short, less turning model number and so on.Silicone mold itself is not Mao, there Maoyou because during operation adds composite silicone oil (silicone oil and white mineral oil complex ligand) as white mineral oils are petrochemical products, not silicone.Mold is not acid, intolerant agingIn the process of making silicone mold, we recommend that customers with the best without any silicone oil, if desired, the amount of silicone oil added up to no more than 5% to 10%. Because of the excessive amount of silicone oil will destroy the molecular weight of the silica, so out of the mold will produce acid, intolerant aging phenomenon.Surfaces of the molding marks, streaks and rough and soThis phenomenon is the product or model to be copied no grinding or polishing sake. Because in fact the model or the product itself is not smooth enough or perfect, so the product or model to be copied if not polished or polished, even the best silicone mold will do pretty, it is not smooth enough. Another case is, when the release agent in the fight, not even brushing can also cause mold is not smooth.How plating silicone mold cleaningElectroplating mold can not go to be cleaned with ordinary sand blasting method, should be using a local dirt cleaning, is generally used to clean up those individual parts plating mold accumulated dirt needs to be cleaned, if it is the mold from the vulcanizing machine removed, then it is more a waste of time this time we just through chopsticks, long strips of wood and other small wooden stuff to scrape the dirt inside the cavity, the use of wood stuff to remove the dirt because of the hardness of the wood is relatively low, it will not hurt the surface of the mold silicone products pure water to dilute the same time we can with the amount of caustic soda plus 10 times, and then take a cotton swab dipped in dilute aqueous base sheet to wipe the dirt to fall off; plating layer.Or go full-mold dirt cleaning method, plating mold on the silicone products vulcanizing agent or an oven heated to 160 ℃, and then press the caustic soda and water ratio of 1: 100 of the caustic soda into the boiling water and mix well, then will pour in the liquid with a good mold, while copper brush to wash dirt off so that the cavity surface, brushing process continues pouring liquid, to avoid mold and dried. After the scrub clean, flush with water mold, so that the liquid is completely clean, air gun and then quickly dry the mold surface water. The entire operation should wear protective gloves to avoid scalding.Condensation silicone mold silicone mold and processing What is the difference editorCondensation-type silicone mold can be cured at room temperature, 8-24 hours into the elastomer. You can accelerate the increase in the amount of curing agent. The increase or decrease in the curing agent. Higher temperatures and humidity, curing faster.Plus RTV silicone mold: condensation-type silicone mold lower strength, the latter a higher strength. Its mechanism is based on silicon hydrogen sulfide vinyl (or allyl) silicone raw rubber end groups and the crosslinking agent molecules on the addition reaction (hydrosilation reaction) to complete. In this reaction, containing a hydride-functional polysiloxane is used as crosslinking agent (curing agent) chloroplatinic acid or other soluble platinum compound used as a catalyst. Sulfurization reaction is carried out at room temperature. It does not release byproducts. Since the cross-linking process does not release low molecular weight compounds, so add molding RTV silicone rubber does not produce contraction in the vulcanization process. This class of vulcanized rubber, non-toxic, high mechanical strength, excellent hydrolytic stability (even under high-pressure steam), a good low compression set, low flammability, the depth of cure, and cure rate can be used to control the temperature, etc. advantages, it is a kind of silicone rubber at home and abroad to develop, in addition, to change the amount of curing agent, curing speed will not change, but will affect the physical properties after curing is complete. Therefore, the measurement of the curing agent must be done as accurately as possible.Select Edit mode mold silicone mold and die selection linesSelect the choice of form and mold parting line is very important,First, in order to facilitate moduloSecond, the parting line should be selected without affecting the overall effect of the productThird, do not affect the quality of products, such as water features series-mode line position is too high, seal the parting line when the material to be more prone to cracking products; fourth is to reduce the flow of operating procedures, such as open mold half.To prevent the flow around the silicone mold species with a wooden plank or a fixed rule in the range, when the opening piece mold with wood and sludge separated that part of the first to open, requiring between sludge and mold species no gap, sludge surface smooth. After the above-mentioned preparation work completed, followed by plaster mold or mold species coated with petroleum jelly or spray release agent on smooth product requirements with a clean cotton cloth soaked in Vaseline evenly coated in the mold species, held for 30 minutes to die kind fully absorb Vaseline, and then a clean cotton cloth to clean the surface of the mold species require bright surface; and as long as the product has a texture evenly coated with Vaseline on it will be better formulated silicone tune. When silica gel formulations should be random directions while stirring, a curing agent and silicone mix thoroughly to minimize the air mixed in gel, smooth product is best applied when the vacuum pump once the first layer of glue, holding the vacuum requirement -0.1Mpa 7-8 seconds.Silica gel with a good timely molding. The glue in a way trickle down in the highest parts of the mold species, let the natural flow, flow not in place by painting brush in place, if the piece is not only full of mold silicone brush evenly throughout the product but also on clay. Each product brush at least three layers each layer of silica silica thickness of 1mm, silica gel in the brush process, requires curing after each layer to another layer of the brush when the brush is applied to the third layer on top of a second layer layer of gauze to increase the strength of the silica gel. The entire mold silicone products based in part on the size of the different requirements for thickness control in 3-4mm, width no greater than the product width 60mm. Silicone start setting time was 20 minutes.1, the master mold dry cleaned, for the smooth handling (can play a layer of mold release wax or brush one release agent)2, 500-1000 g of silicon rubber mold (silicone mold, plastic mold, silicone rubber, silicone) Sheng such as plastic pots spare;3, after the hardener by weight ratio (typically 1.5-2.5%) were weighed into a container for mixing, stir;4, depending on the situation (in particular, the first layer) by adding a certain amount of silicone diluent. Until thoroughly mixed so far, usually 3-5 minutes.5, mixing silicon rubber mold (silicone mold, plastic mold, silicone rubber, silicone) and hardener, the reaction was carried out at room temperature, that is, and the release of low molecular weight alcohol, the alcohol molecules from the colloid as required under negative pressure discharge bulbs 1 -3 minutes. Also available (depending mainly depends mold division operating experience) without the aid of the device 6, the multilayer sheet molding brushing should follow the inner, middle and outer while curing is appropriate. Curing agent is relatively small, the reaction time is lengthened, the full response, colloid like, thus curing agent is preferably within less foreign and more. Brushing until the first layer (inner layer) dry and then brush the second layer. Operating time 30-50 minutes, the removal time 10-15 hours. Curing time of 24 hours. Note brushing first, such as gauze after the best two-story addition, which can greatly improve the mold life (but must not use fiberglass cloth, or likely to cause the hierarchical leaving the entire mold scrapped)7, three-dimensional perfusion mode, generally 10-15 hours curing as well.8, but also of plaster or fiberglass outer mold produced after soft to support the soft silicone moldnote:1, line selection mode: Select position does not affect the appearance of the product; choose a location after grouting easy processing; mold itself is easy to select the form removal position; select the product easily deformed position2, must not be in a hurry to increase the amount of the production schedule and blind hardener, otherwise it will greatly reduce the life of the silicone mold.Market outlook editState silicone downstream industry development present polarization. The presence of silicone monomer in the domestic anti-dumping protection policy context, in recent years, domestic enterprises launched a large monomer production capacity, these products can enter the concentration of the release period in 2009-2012, industry monomer production capacity phased excess; but the downstream deep-processing product development is slow , thus making the downstream processing enterprises continue to get high profitability, while different from the international market in an integrated enterprise-based industry characteristics.From the development path of the domestic enterprises in terms of silica gel, single monomers and intermediates business is difficult to achieve sustained and stable development, we can not avoid the impact of price volatility. After obtaining competitive advantage and the ability to have the financing to complete the layout of the leading enterprises in the field of the monomers, are actively expanding downstream products. Future enterprises Monomer / Intermediate internal digestion ratio will increase substantially corresponding to a monomer / intermediate amount of goods will be significantly reduced, and the transfer of profits from the industry to the whole field of downstream processing industry comprehensive income, profitability and integration ability to hedge risk gradually. With the rapid development of the domestic industry, the demand will increase the mold, silicone mold market potential will increase!Entry Label:Non-life, life, industrial products
- Previous [Return Home] [Print] [Go Back] Next
Products Search
Brand Zone
Contact Us
Contact Person:
Xiaohai QiTel:
+8613533634945Fax:
Renewable resources, reasonablyE-mail:
158354113@qq.com-
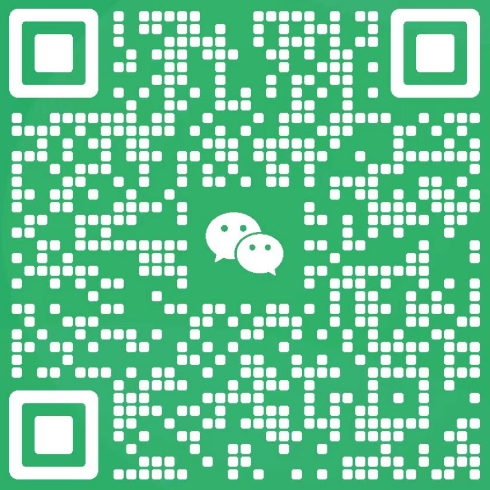