News
- 2016-11-23 16:10:12
-
Injection molding silicone
A, injection molding, silicon is introduced
LSR injection molding liquid silicone rubber is a two-component heating vulcanization silicone rubber, is a transparent or translucent sticky liquid, belong to forming a. Compared with condensation type liquid silicone rubber with vulcanizing process does not produce by-products, little shrinkage, can the advantages of deep sulfide, sealing at high temperature is better than condensation type; And than the mixed silicone rubber, silicone injection molding small molecular weight, low viscosity, easy to processing molding, saves mixing, preforming, and finishing process, easy to realize automation, and can save energy and labor, short production cycle and high efficiency.
Second, the injection molding silicone features
1) it's a two-component, high transparent, high strength and high tear.
(2) without being limited by the thickness of the products, but the depth solidification.
(3) low shrinkage rate, not emit low molecular crosslinking process, so the volume, shrinkage rate is less than 0.1%.
(4) good liquidity, easy injection, excellent thermal stability and the cold resistance (using the temperature - 50 ℃ ~ 250 ℃).
5. Excellent resilience, yellowing resistance, heat aging resistance.
6 key life can reach more than 10 million times.
Three, use the injection molding silicone
Injection molding silicone is mainly used in injection molding process, services, signs, jewelry, computer keyboard key, kitchen utensils, duplicator, farm machines and other printing equipment, rubber roller and other miscellaneous pieces of silicone seal design application and production of special purpose products, bottle, pacifier, also applies to the nipple, goggles and other gear grinding plate, finger toothbrush and laryngeal mask, fork tubes and other medical products.
Silica gel nasal bracket
Silica gel nasal bracket
The silicone pacifier
The silicone pacifier
The silicone keypad
The silicone keypad
Four parameters, injection molding, silicon technology
Model appearance hardness (Ao) viscosity (Pa s.) density (g/cm3), tensile strength (Mpa), elongation (%) tear strength (KN/m) purposes
RXD4420 transparency 20 A: 700 B: 700 1.07 6, 600, 28 is suitable for making the pacifier bottle, pacifier, grinding plate, goggles and other gear, finger toothbrush and laryngeal mask, fork tubes and other medical supplies
RXD4430 transparency 30 A: 700 B: 700 1.07 6, 600, 38
RXD4450 transparency 50 A: 1000 B: 1000 1.12 8.5 450 43
RXD4470 transparency, 70 A: 1000 B: 1000 1.15 8.5 300 38
RXD5530 transparency 30 A: 700 B: 700 1.07 6 500 25 is suitable for the production of kitchen supplies, copiers, printers rubber roller printing equipment, and other miscellaneous pieces of silicone
RXD5550 transparency 50 A: 1000 B: 1000 1.13 7 400, 35
RXD5560 transparency 60 A: 1000 B: 1000 1.13 8 350 40
RXD5570 transparency, 70 A: 1000 B: 1000 1.15 8 250, 35
RXD7740 translucent 40 A: 70 B: 65 1.09 4 300 10 is suitable for the key, notebook computer manufacturing
RXD7750 translucent 50 A: 75 B: 70 1.1 4.5 280 11
RXD6640 semi-transparent mixed 40 viscosity 45 A: B = 10:1 5.5 300 20 applies to clothing tag, design, craft jewelry, and other fields
RXD6650 translucent 50 mixture viscosity 130 A: B = 10:1 June 25 350
Fifth, silicone injection molding process
Injection molding is a manufacturing process, is to point to have certain shape model, through pressure will melt soluble state of colloid touch cavity, liquid silicone injection and molding, process principle is: the solid silica gel, through the pressure of the injection machine, injection mould with a certain speed, die through channel cooling cavity will get the silicone curing and design the same product. It is mainly used for thermoplastic molding, also can be used for thermosetting molding.
The silicone injection molding process flow chart
1, the preparation for molding
In order to make the injection molding smoothly and ensure the quality of products, production before the need for raw material pretreatment, washing machine barrel, preheat insert and choose to release agent and a series of preparations.
2, the injection process
Injection process generally includes: charging, plasticizing, injection, cooling, mold release.
(1) material: due to the injection molding is a batch process, and therefore should be quantitative (constant volume) feeding, to ensure the stable operation, plastic uniform plasticizing, finally obtain high quality plastic parts.
(2) plasticizing: molding material in the injection machine machine barrel after heating, compaction and mixing effect, a loose powder or granular solid into a continuous process of homogenization of the melt.
(3) : injection piston or screw from the barrel in the measuring position, by injecting oil cylinder and the piston under pressure, good plasticizing plastic melt after barrel front end of the nozzle and mold in the process of pouring system rapidly into a closed cavity. Injection and fluid can be subdivided into molding, pressure maintaining feeding, go back three stages.
(4) cooling: after the pouring system of plastic and freeze, continue to pressure is no longer needed, so can be returned to the piston or screw, remove the plastic melt pressure inside the cylinder, and add new material, at the same time in the mold flux into the cooling water, oil or air, such as cooling medium, to further cooling of the mold, this phase is called the gate freeze after cooling. Cooling process actually starts from plastic melt into the cavity, and it includes from mold filling, the holding to the stripping of this period of time.
(5) release: can open mould plastics cooled to a certain temperature, the launch mechanism under the action of outside will launch mold plastic parts.
3, products of post-processing
To eliminate residual stress: (1) annealing; (2) : wet color, plastic properties and dimension stability.
Six, injection molding silicone use matters needing attention
1, take the tool to distinguish between A and B agent or try to wipe clean before use, avoid mixed partial agglomeration and cannot be used properly.
2, A and B component after all, it must be finished within 72 hours.
3, when used to avoid mixed with acid, water, alkali, strong oxidizing agents, avoid and contain N, S, P, Sn elements such as compound contact, otherwise it will cause the product is incomplete sulfide or sulfide.
- Previous [Return Home] [Print] [Go Back] Next
Products Search
Brand Zone
Contact Us
Contact Person:
Xiaohai QiTel:
+8613533634945Fax:
Renewable resources, reasonablyE-mail:
158354113@qq.com-
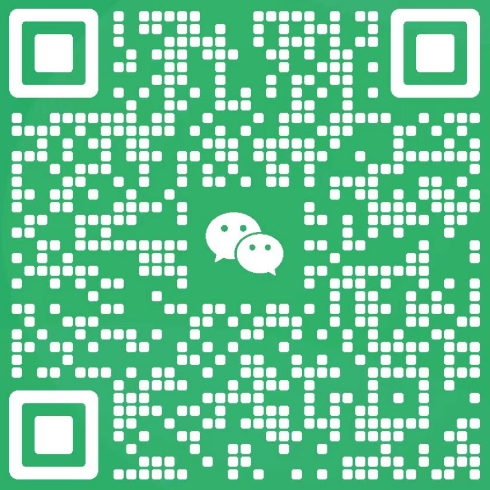